|
 |
MANUFACTURING
ProCESS OF PRime
Gold THERMEX TMT BAR |
 |
|
|
The Billets are reheated at a temperature 1200°C in the re-heating furnace and are rolled into specific sections of bars, required. After passing through finishing stand, bars are entered into a Thermex cooling system, where they are kept till the outer surface of the bars becomes colder while the core remains hot. This creates a temperature gradient in the bars.
After the intensive cooling, the bar is exposed to air and the core re-heats the quenched surface layer by conduction, therefore tempering the external martensite. When the bars are taken out of the cooling system, the heat flows from the core to the outer surface, further tempering of the bars, which helps them attain a higher yield strength. The resulting heat-treated structure imparts superior strength and toughness to the bars. |
|
Cooling
process
is
illustrated
below: |
|
|
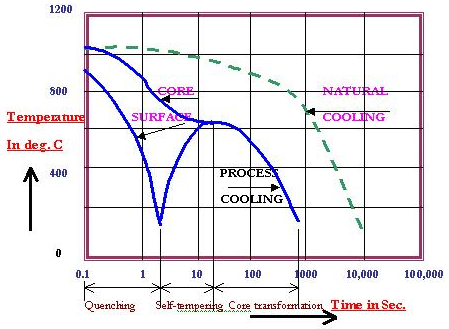 |
|
The pre-determined cooling of the bar periphery transforms the peripheral structure to martensite and then annealed through the heat available at the core. The peripheral and core temperature difference finally equalises at around 600°C and the resultant bar structure is of tempered martensite at the periphery and of fine-grained ferrite-pearlite at the core.
The resultant soft core forms about 65-75 per cent of the area (depending upon the desired minimum yield strength) and the rest is the hardened periphery. The equalizing temperature together with the final rolling temperature is the most important parameter to achieve the required mechanical properties.
Finally, when the bar is discharged on to the Cooling Beds, the remaining austenite transforms into a very fine-grained pearlite structure. |
|
|
|
The
figure
below
illustrates
a
typical
TMT
bar
manufacturing
process: |
|
|
|
After this process of thermo mechanical treatment, a dark etched peripheral rim of tempered martensite and a grey core of ferrite pearlite get formed. The tempered martensite surface layer is very hard while the microstructure of the core is a very fine-grained ferrite and pearlite which is quite soft. The result is a structure with a high yield strength combined with high ductility. |
|
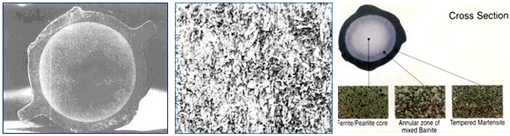
|
Microstructure of TMT bar showing peripheral rim of tempered martensite & core of ferrite pearlite get formed |
|
Tempered Martensite Rim |
|
|
|
TMT bars are also known as 'Quenched and Tempered rebars', because of the quenching and tempering processes involved in making the bars.
The production of quality TMT bar depends on three major factors - quality of raw materials, a properly designed and automated mill, and a well-designed quenching and tempering technology. |
|
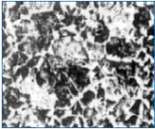 |
|
|
TMT bars having uniform and concentrated hardened periphery and the softer core will have the desired tensile strengths coupled with high elongation as required in seismic zones. Depending on the size and grade, rebars with hardened periphery of about 15 to 30 per cent of the cross sectional area of the bar are ideal for civil constructions (constructions of houses, offices, etc.) |
|
|
|
|
|
|
|